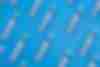
Plastic and rubber
Discover moreSmart Factory in the Plastic and Rubber Production
The plastic and rubber sector is, without a doubt, one of the most important because of the wide range of products and components it produces, from everyday consumer goods (plates, cutlery, containers, lids, etc.) to highly technical items (fittings, gears, seals, tyres, and more) used in almost every sector (construction, industrial, food and beverage, automotive, just to name a few).
In recent years, companies working in these sectors have become increasingly committed to improving the efficiency and sustainability of their processes through technology innovation and cost control.
With the integration of finite capacity scheduling, data collection and maintenance management for machinery and equipment (e.g. moulds and dies), the MES system is an essential tool for these companies, enabling:
the needs of the industry
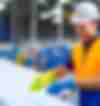
The main problems that a factory in the plastic and rubber production sector must face are related to the management of production departments and improving efficiency overall of the company.
Production management needs to be improved from the beginning of the processing process to its end. Initially, through traceability, the raw materials and materials needed for the production of the product are identified. Machines must be constantly monitored, both for temperature and for the maintenance of dies or moulds. When you have the finished product, it is important to know its composition and storage, to identify it and to have total control over the production process.
The efficiency of business productivity is achieved by connecting machines in 4.0 mode and beyond. Through preventive maintenance management, machine downtime and production problems can be reduced. By providing real-time data, you can cost the production for each individual process and have total control over consumption. To keep up with the current plastic regulations, an interconnected factory in an Industry 4.0 perspective can collect detailed information on energy consumption and can optimally manage production waste, reusing the scraps to have a greener product, maintaining the same quality.
Download our institutional brochure
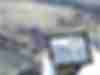
Tesar for the plastics industry
To ensure better production management and better business efficiency, Tesar offers some solutions that allow you to facilitate automation and accompany companies during this technological transition, connecting all machines in 4.0 and beyond. In particular, by installing some of its flagship software in the departments, such as Motis2 (MES software for production management) and Sicop (quality management software), to which is added the module traceability I4Traceability and the module I4Energy for monitoring quantities and consumption. These data can be consulted in real time via the TS400 department terminals.
Connection to machines/plants
by means of the most common electromechanical protocols or signals
management
multi-print moulds
tracking
of the life of moulds and dies
Management of maintenance of machines and equipment
Depending on actual use
Recording machine parameters
For the performance analysis
traceability
the materials used and their origin
management
Of waste and regrind
Detection and monitoring of energy consumption
with cost allocation on work orders
Scheduling at finite capacity
depending on different optimization parameters
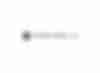
Maxima Gradi S.P.A.
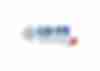
LU-VE S.p.A.
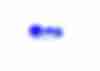
Off. Meccanica Torneria Gastone Berni S.R.L.
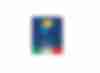
Scatolificio Vec S.R.L.
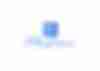
Paglieri S.p.A
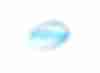
Torneria P.M.S. S.R.L.
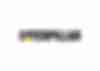
Caterpillar
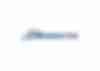
Unidelta
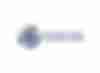
I.T. International Transmissions S.A.
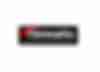
Tormatic S.R.L.
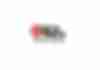
Abra Beta
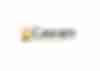
Casram S.A.
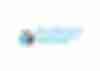
Trafimet
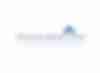
Trafilspec – I.T.S. S.p.A.
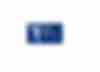
Vic viterie Italia Centrale S.R.L.
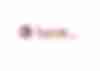
Berra S.R.L.
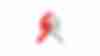
Torneria Serra S.R.L.
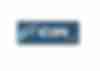
C.R. S.p.A.
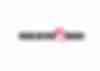
Rexnord
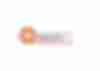
I.M.P. Pasotti S.p.A.
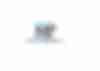